Before Consideration:
A general guide is difficult to be provided here. The spectrum is always related to customer's need. As a coating OEM producer, we should try our best to achieve your goal. We will not decide the final spectrum used in your product. Customer should and will be the final decision-maker. However as a OEM producer for coating vendor, the coater has its own inherent ability. It may not be able to do anything you want. Detailed discussion between customer and vendor are needed, please contact us for further information.
After customer describe his need ( usually to descibe a spectrum profile, see below) , we will use simulate sofeware to analysis the coating layer composition (the substrate glass will be considered in its optical aspect). Analysis ok, did not mean we can do the filter successfully. The coater has its inherent limition. The controll method, precision (time controll, crystall controller, optical monitor controll), vacuum ability, added ion source, rotating dome, .... ect. It has to discuss case by case. Please also reference to Communication Flow chart.
How to communicate?
1. 1. Explanation of your products:
Most customers inquire coating OEM producers in first time communication usually begin with "can we make certain specification's optical filter". The specificaiton which customer provided is usually from co-worker or friend. Such inquiry will usually end quickly and only a little progress. But if you can tell us "what is your application and what you are trying to accomplish", we can make a more appropriate suggestions to you. If you directly adapt other's specificaiton, you will make same product like others. The cost you saved only form our good processing efficiency and an economic overhead fee. Customers usually hope to cost down form existing optical filter hugely. The specification you provided may be to good to your application. There are many alternatives could be choose to cost down. If the tolerance of T50% can be released a little, the price may be reduced 15-30%. Maybe the wavelength interval shift a little, the price may reduce. It will be very helpful to cost down your products, if you can tell us "what is your application and what you are trying to accomplish".
2. The coating type:
Form practical experience, vacuum coating industry has classified the product into several catalogues. Each type has it own cheracteristic. Please reference to our product catalogue, such as AR, UV, IR, Hot Mirror, Cold Mirror..... There are some existing requirements to certain product types. If you can point out what type your product is. Coating producer will help you to consider some properties you may not know.
3. Wavelength Range:
Make thin film layers on filter is to deposite a different optical index material on substrate, use physical interference to enhance the transmission or reflection of light at a certain wavelength. With the spectrum of light, three regions is classified as Ultra violet(UV), Visible, and Infrared(IR). The UV range is 200-400nm. The visible range is 400-700 nm. and eccomposses the human eye detection. The wavelength range above 750~ are classified as IR range. It is a very wide range can expend to 12000nm.
All coatings can be classified as broadband (wide band) or narrowband (nano band). A broadband covers a wide range of the spectrum. The optical filters cover or handle the light with a wider wavelength range will be more expensive than narrow ones. the number of layers of broadband filters are more then the narrow band filters. The producer need more quantity of target material and more processing time to produce the filters.
4. Transmission or Reflection characteristics:
Reflection and transmission are join together and measured as percentage of transmission. Which refers the light energy passing through a substance (glass). From 100% (total passing through) to 0% (total rejecion, No light pass) present the passing engery level of transmitting light.
Before communicating to coating OEM vendors, understand the transmission graph is important. This is the most important tool media for customers and vendors.
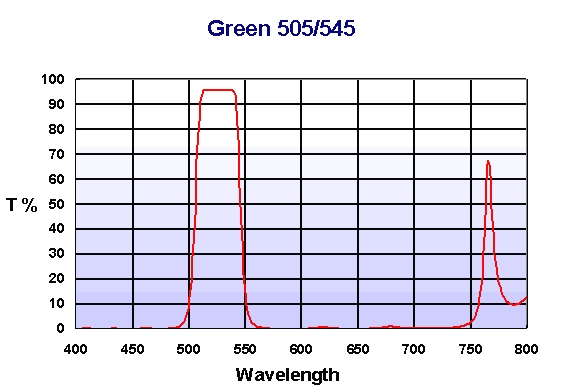
For the spectrum paragraph showed above, there are some specifications will be defined
Pass Band: 560~750nm Tabs >90%
This is the target of high transmission wavelength interval of a pass filter.
Stop Band: 400~490nm Tabs<3%, 560~700 Tabs<3%
The reflection or absorption wavelength range by the filter. Low light transmittance required.
Wavelength interval: for this case 400~700 visible wavelength required.
400~700nm in visible range, 200~400nm in UV range, 700~1200nm in Near IR range. It is the work range of your filter.
Half transmittance position, T50: T=50% @ 505 +/-10nm; T=50% @ 545 +/-10nm
It usually defined as an acceptable deviation tolerance to your filter spectrum function. It is important to band pass filters. Small of tolerance need more precisely processing control. The yield rate is highly related to this specification.
Slope: It is not required in this paragraph spectrum.
The linear approximation to the cuton or cutoff slope. Usually simplifed to express as 20nm or 15nm. It means the slope must be sharp form 80% ruduce to 20% transmittance in 20nm wavelength.
NOTE:
Tabs: absolute transmittance in specific wavelength range. The transmittance in every wavelength must all higher or lower than the transmittance value required.
Tave: Average transmittance in specific wavelength range. The transmittance value in every wavelength not necessary all higher or lower than the value required, but the average value must pass the specification in this range.
Rabs: absolute reflection in specific wavelength range. The reflection in every wavelength must all higher or lower than the value required.
Rave:Average reflection in specific wavelength range. The reflection value in every wavelength not necessary all higher or lower than the value required, but the average value must pass the value in this range.
5. Angle of Incidence(AOI):
It is important to notify us the Incidence of Angle of light. Since the light passing through the glass with different angle, the deposite thin film is different. If you install the filter in your device with wrong angle, the performance will decrease.
6. Other consideration
US Military standard (MIL-standard, if applicable):
For optical glass or filters, there are amost no any common specification for industry can be followed. U.S. Military seted a series of specification to receive vendor's optical products. Since for military use, the specification and test is rigid for vendors. A lot of test and paperwork is needed. The price for military usage is high due to its high functional and reliabe requirement. For commerical usage, it is only a reference. If you can't find any specification description for your product, Mil-STD is a reference. Following documents is a part of specification for optical products in Mil-STD.
|
Optical Terms and Definitions
|
|
Improvement of Manufacturing Techniques and Quality of Optical Scratch Standards for Fire Control Systems
|
|
Reflection Reducing Coaing for Instrument cover Glasses and Lighting Wedges
|
|
Durability Requirements for Single or Multilayer Interference Coatings.
|
|
Filters, Polarizing (for Optical Instruments)
|
|
General Specifications for Infrared Interference Filter Coatings.
|
|
Mirrors, Front Surfaced, Aluminum for Optical Elements.
|
Working environment:
Today's thin film coatings will add ion source to increase addsive force. It is very durable to most environment. But if your product is applied to extremely temperature or humidity, the substate optical characteristic may alter. Luckly, the science reseach has built a good database. Input temperature or humidity data can get a trustable analysis result.
If your product is applied to acid or alkaline environment, the coating vendor will need to consider the target material. It will be a more complicated problem. Remember to describe your product environment to coating producer.
Quantity :
It is important to any kind of industry producers. The PVD thin film coating uses batch production method. If you only produce one or two batch, the preparation (procruement of substate, prepare fixture, design optical layers...) is same to procuce 100 batches. The preparation cost will to be shared only by one batch. It will cost much. And It is very possible to refuse accept your product if your quantity is too small. If you can accept existing specification filters, It will hugely cost down.
Another issue is production capacity, the coating machine is an expansive investment. The clean room is also cost much. To build production capacity is slowly and must well planned. If your quantity is too big for existing capacity, a detailed requirement rolling up will be required by coating vendors.
|